Overview
Druck, a Baker Hughes company, manufactures pressure sensors that are built for accuracy and precision. We are one of the leading technologies in the world of industrial testing. When it comes to data gathering in industrial applications, there are three key areas to consider: test applications, on-vehicle test, and engine test cells. As a result, our sensor technology has been developed to support some of the most rigorous, challenging, and precise applications.
Druck provides the full solution—from pressure sensors to testing and calibration of test tools. Our pressure sensors can be used in extreme conditions, such as high temperature or vibration, and can be used for test applications. Druck pressure sensors are used for all kinds of vehicles from traditional Automotive to heavy and off-highway vehicles, such as diggers, tractors, and trucks. Our pressure sensors are also developed for high-speed trains, such monitoring pressure in brake control units. We also design pressure sensors specifically for Motorsports.
We at Druck are positioned to support the development of the Automotive industry, such as electric and hydrogen applications, alongside railway solutions and other vehicles developments
Druck’s PACE product line is a modular pressure control system that brings together the latest pressure control and measurement technologies to offer an elegant, fast, flexible, and economical solution to pressure calibration, verification, and control.
Within an automotive testing environment speed, efficiency and reliability is key. Providing all of that is the PACE pressure controller from Druck. Our pressure controllers interchangeable control module translates to virtually zero downtime, as a replacement control module can be quickly fitted to allow pressure range change, calibration, or service.
PACE employs full digital control to provide high control stability and high slew rate while its digitally characterized pressure sensor offers the quality, stability, higher bandwidth, and precision associated with this latest generation of piezoresistive devices suited for your automotive testing environment.
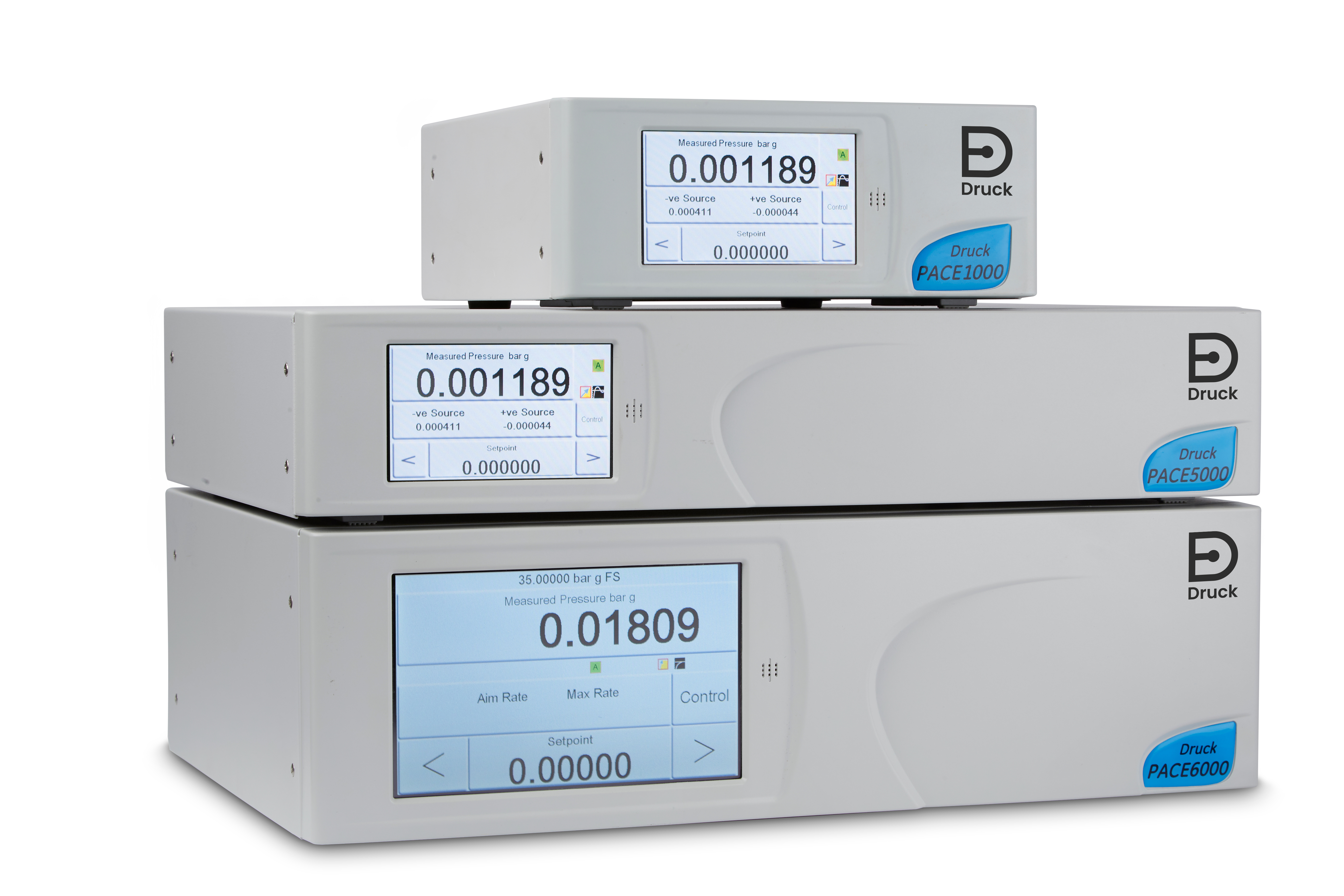
To operate effectively in test applications, you need confidence in the reliability of your instrumentation, which is critical to quality data collection. When faced with rapidly changing conditions, potential unit failures, and extreme environments, durability and robust design are key.
- Accuracy: better than 0.01% FS
- Cost ownership: reduce downtime and optimize processes with efficient, reliable, and cost-effective sensors that are ideal for long term reliability, accuracy, and economical measurement
- Process optimization: CAN Bus communication to enable fewer wiring requirements
- Difficult environments: high shock and vibration
- Test repetition
- Inventory management
- Variation in pressure
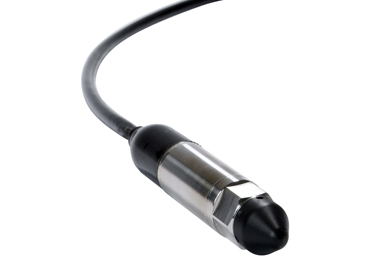
Titanium or stainless-steel metal work with appropriate cable corrosion can be chosen to reduce the risk of chemical damaging sensors. This translates to a pressure module that provides:
- Great media compatibility with corrosive chemicals
- Gauge, negative gauge, absolute, and differential references that allow you to measure in the way that suits you.
Small size, fully welded construction and high-quality cable connections mean our products give reliable operation in hot and high vibration environments, giving you reliability, accuracy, and stability when you need it the most.
By integrating proven Druck technology, we offer CAN Bus protocol with up to 127 sensors on a single Bus. Such features reduce installation time as well as infrastructure costs, reducing your cost of ownership and streamlining processes.
To ensure the excellent speed, efficiency, and reliability of your automated pressure control infrastructure, high-speed modular pressure control systems are critical to your operations, particularly when time is a factor. Because of this, we designed our PACE product range with process optimization in mind. Features such as an interchangeable control module translate to virtually zero downtime, helping you to save time and increase productivity.
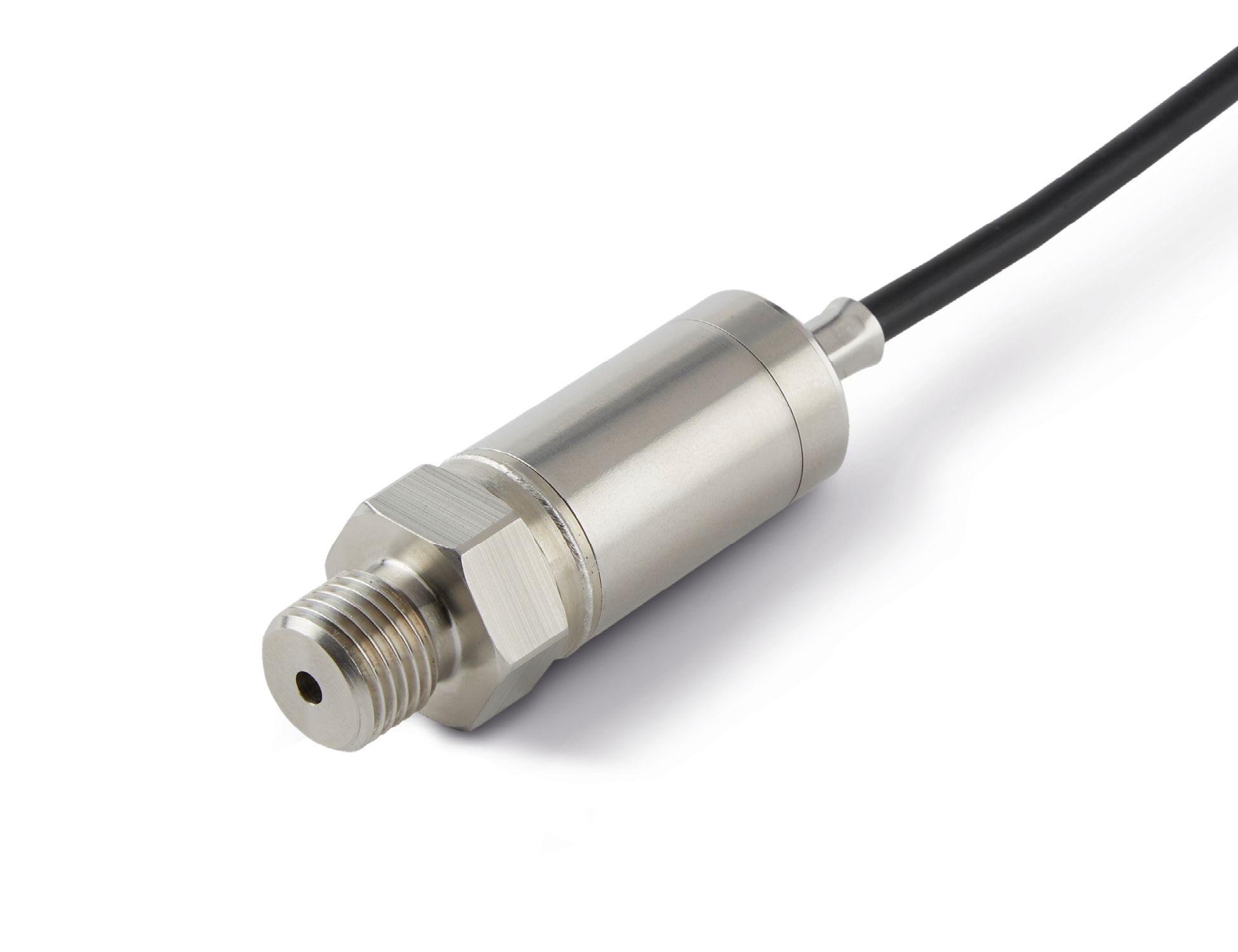
On-vehicle testing means dealing with limited space, rapid changes in temperature and high vibration environments. Managing your instrumentation effectively in such conditions requires speed, precision, and accuracy.
From traditional Automotive test cars to Motorsport performance vehicles, Druck’s Industrial and Motorsport pressure sensors deliver the data necessary for your decision making.
Druck offers pressure sensors that are small (25 mm, 17.5 mm, 12.5 mm) and light enough to be located on machines for testing that eradicate the need for additional expense and delayed readings associated with piping out pressure. Additionally, our cables are mechanically robust and immune from electro-magnetic interference.
Digital compensation allows for overall accuracy of 0.1% that can be maintained over wide temperature ranges. The use of high-quality electronic components give you a range of options to accurately measure temperature ranges from-40°C – +175°C. On-chip thermal compensation ensures accurate data in the face of extreme conditions and rapid changes in temperatures to 0.01% full scale.
Fully welded construction in high-quality materials, potted electronics, and high-quality cable sheathing ensure both the highest IP rating and reduce the risk of damage. This gives high shock and vibration protection in addition to Industrial EMC protection to electrical noise, which provides many years of service in environments with high levels of:
- Vibration
- Shock
- Humidity
- Electrical noise
- Temperature variation
Helping the Automotive Industry Succeed

No, ADROIT6000 and UNIK5000 are complimentary sensors for slightly different applications. Our engineers are ready to help you understand which sensor better suits your application. Contact our technical team for more information.
No, there are many versions of UNIK5000 that are not replaced by ADROIT.
Testing applications. The ADROIT6000 makes buying a high-performance sensor easy.
ADROIT6000 meets a need for digital accuracy without the overhead of digital communications present in DPS5000 for other applications
Great question with potentially a long answer, but in short, both sensors provide an analogue amplified output; however, the ADROIT uses digital processing to enable it to provide an improved level of accuracy across temperature.
The ADROIT is also smaller at only 19mm diameter against the 25mm UNIK. The UNIK being all analogue provides a faster frequency response and is also available as an mV output. There are several other differences as well. Our sales team would be happy to assist in making the best choice for your application.
Pressure sensors are subject to many sources of error, and many manufacturers state the error in different terms. Druck uses two descriptions of error based on the technology. The UNIK5000 is an all-analogue pressure sensor, and the errors are split into three terms: NLH&R (non-linearity, hysteresis, and repeatability), zero/span setting, and thermal error. The total error can be calculated by taking the root of the sum of the square (RSS) of these components.
For our digital processed sensors, we make things very simple for our customers by stating a single maximum error value which includes all sources of precision error affecting the sensor. Druck always states maximum error values, so in practice, the sensors will be much better than stated. Beware that some companies state the error as typical figures, meaning the product you receive may not be as good as stated.
Visit our product pages and UNIK configurator page. You may also speak to a specialist in your area.
Visit our product pages and UNIK configurator page. You may also speak to a specialist in your area.