Highlights
Highlights
Benefits
- Lower operating costs as a result of high efficiency and energy savings
- Centerline mounting feet increase thermal-expansion tolerance
- Hard coating on all mating surfaces of stage seals and balancing drum to increase life
Features
- Clearances and tolerances between rotor and stator parts enable frequent starts and stops with rub-free operation
- Diffusers and return channels are precision-casted and machine-finished for high conformity and low radial loads on the rotor
- Double, symmetrical balancing flow lines minimize axial thrust variation and eliminate asymmetries that cause vibration
Applications
- Boiler feed in power generation plants
- Reverse osmosis
- Energy recovery, CO₂ injection
Overview
Our DDHF-R multistage centrifugal pumps are designed for the requirements of several services including boiler feed in power generation plants, pipeline, reverse osmosis, energy recovery, and CO2 injection.
This pump family is designed to work in a demanding environment, delivering pressure as high as 350 barg, withstanding process temperatures up to 250°C, and managing flows close to 1,000 m3/h with an extremely high level of reliability and efficiency (over 85%). Based on the above, a single train's installed shaft power can approach 10 MW in a high-speed arrangement.
Optimized performance
To maintain such high performance with a short warm-up time, this product uses innovative materials—mixing alloyed steel and composites—and a unique layout with thermal guides and baseplate specifications tailored to customer requirements. The inlet channel is designed to optimize flow uniformity and reduce the net positive suction head required (NPSHR) during transient and steady state operations.
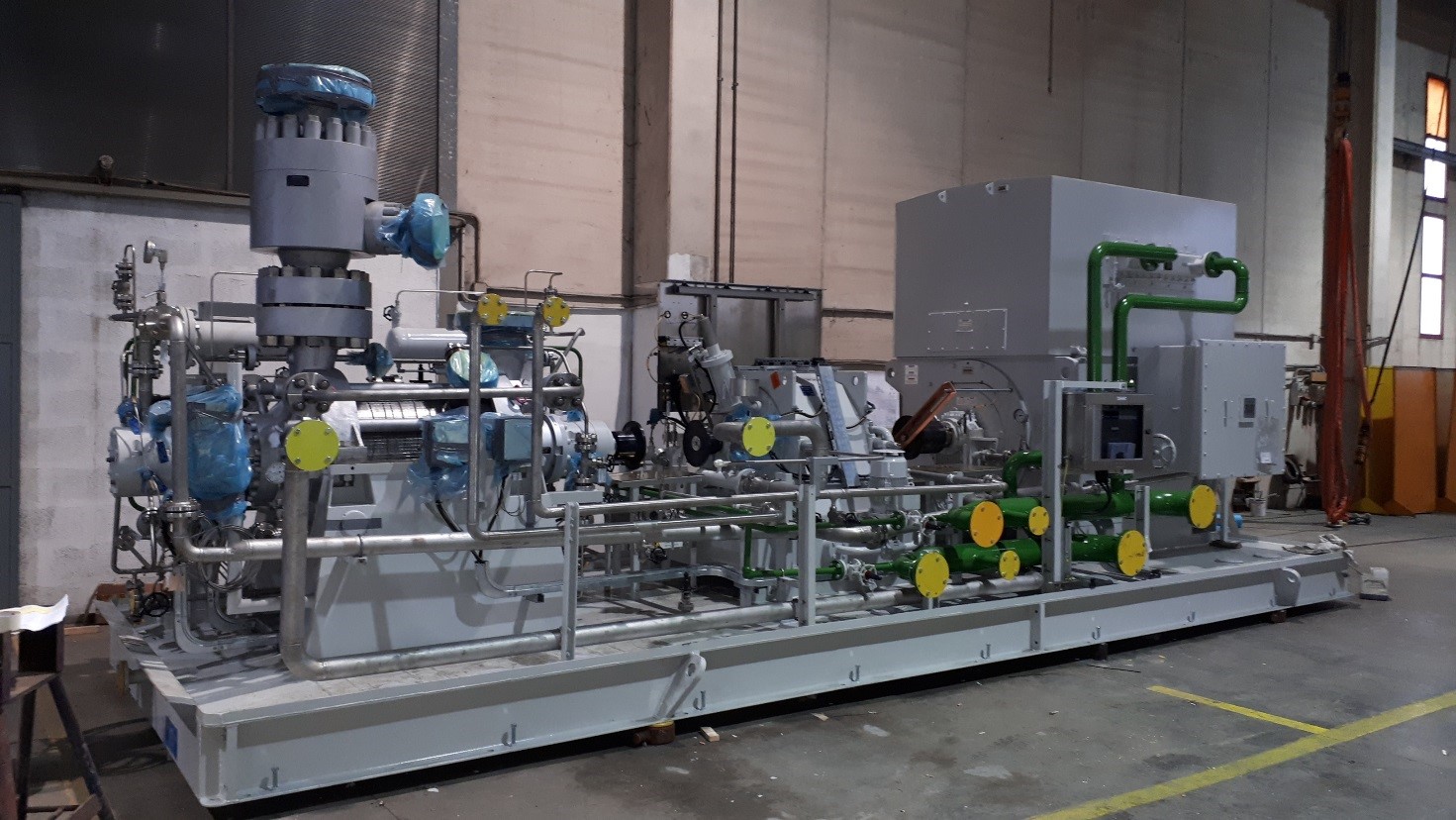
Other key features include a rotor that can operate below its first critical speed to increase reliability and life of seals, a shaft stepped to facilitate mounting of impellers, and ISO G1 balancing grade available up to six stages. To maximize performance predictability and hydraulic radial load balance, the impellers are precision-casted and shrink-fitted to avoid fretting and residual unbalance. The first-stage impeller is available with single or double suction.
The pump is part of an integrated pumping solution that includes an electric motor, sealing systems, and lube oil console located on a common baseplate; machinery control instrumentation, automatic recirculation valves (ARVs), variable-speed driver system (VSDS), and machine monitoring system (MMS) that can be adjusted to best fit user needs.