What quality means and what you’d do to achieve it is not the same for every company. Read how a new quality leader is committed to a radical rethink.
“For me, quality is about viewing everything through a different lens compared with the past, challenging the status quo and elevating aspirations in every part of the business,” says Charles Lawrence, the new Global Quality Excellence Leader at Druck, a Baker Hughes business producing pressure sensors for just about every sector on the planet, including energy, aerospace, automotive, environment, healthcare, water, metrology, environment, electronics, and many, many others.
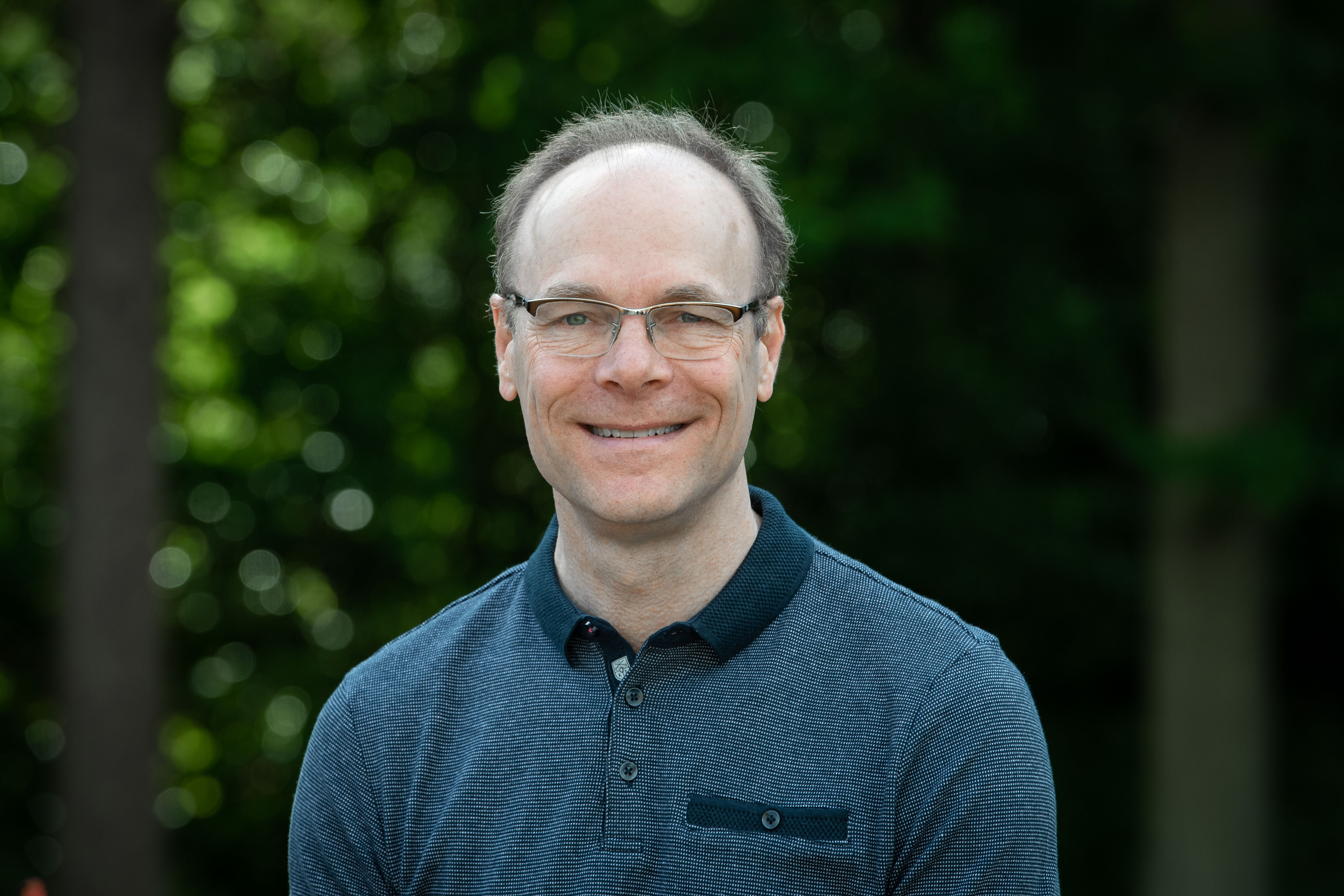
There’s tension in the term “quality”. Its interpretation depends on perspective, and customers for any product naturally assume that the manufacturer will strive for zero defects, which is often a starting premise of product development but not simple to achieve. The concept of “quality control” invokes even greater ambivalence with its implied policing of practices. Employees can easily view it as a requirement to conform rather than feeling they have the agency to change things for the better.
The company’s customers rely heavily on the accuracy and resilience of its pressure detection and measurement instruments. Lawrence says his proposal to work differently towards quality improvement has been met with “great openness and willingness”. The dedicated team of 800 global employees mostly operating from the UK is, he adds, imbued with “a lot of pride and a lot of capability”.
Lawrence has contributed to quality excellence in a number of other already high-performing companies throughout his career so far. His modus operandi is to break down self-limiting beliefs and “lift the lid” on what could yet be achieved.
“We tend to convince ourselves that what we did yesterday is probably what we’ll do today, rather than believing that we could do things better, and perhaps even radically differently tomorrow,” he says, adding, “When we get wrapped up in the day to day, and we’re busy, we stop seeing the possibilities, so every now and again, you need an external perspective.”
Several months into fulfilling his new role, Lawrence is that deeply interested and observant outsider with a passion for enabling people to take satisfaction with their work to new levels. Although he and his team of 10 quality engineers engage throughout the business, and Lawrence has complete accountability for the entire value stream, he says the company’s leadership team is key to implementing a quality-centric culture.
Key ingredients of a zero-defect culture
Leaders who articulate a belief in zero defects, who are committed to design processes that enable as many faults as possible to be ironed out before the manufacturing line itself is designed, who resource their teams to rethink legacy procedures, and who acknowledge and celebrate incremental improvements are critical to achieving step changes in quality.
The teams have so far identified a couple of opportunities to implement beneficial changes to production, and Lawrence says the point is “not to go all hot and heavy on what’s potentially being done wrong” but to ask people at all levels of production, “What have you noticed?”, “How can we help you improve it?” and “What do you need?”. He adds that celebrating successes every quarter and demonstrating to all employees how processes and, therefore, products have been transformed can also contribute to “a complete change in the company-wide mindset”.
Celebrating successes can contribute to a complete change in the company-wide mindset
Charles Lawrence, Global Quality Excellence Leader
This approach might also be articulated as “Go see. Ask why. Show respect”, one of the basic adages of “Lean manufacturing” as exemplified by Toyota and subsequently adopted by businesses in many industries across the world. It’s also built on use of data, process control and improvement, promoted by legendary American engineer, statistician, and management consultant W. Edwards Deming whose teachings are credited with driving post-World War II Japanese manufacturing to world-beating standards of quality and cost competitiveness. It has since been incorporated in the Six Sigma management tools honed by Motorola in the 1980s to improve company capability and the quality of output.
Interestingly, Lawrence’s obsession with fostering quality was kindled when his first employer sent him as a young engineer to work with Ford — the first US company to enlist Deming as a consultant to improve its operations in the early 1980s, on the basis that if Japan could do it, why couldn’t they?
“Having had that experience at Ford, I saw the power of getting things right the first time, rather than reworking — with all the complexities that it entails,” he says; “This approach got me interested in quality excellence.” Most companies work on a combination of legacy and newly developed products, and since 80% of the cost of a product is set by the initial design, it's important to engage early on excellence. On the other hand, says Lawrence, it can be easier to identify how existing products could be better, “because you can see what’s wrong and go after the tactical things to fix”. There are opportunities and challenges in either product phase.
Workforce diversity contributes to every aspect of company achievement
Lawrence builds on the “Go see. Ask why. Show respect” principles to value different perspectives and different skill sets as embodied by a diversified workforce. Since joining the company, he has become a leader of Baker Hughes’ Enabled Employee Resource Group (ERG), which supports greater diversity, equity, and inclusion in all aspects of corporate hiring and operations. The Enabled ERG specifically champions hiring and supporting employees with disabilities. For more information about diversity and inclusion initiatives, read here.
Lawrence also describes it as “building confidence in people who often don’t have confidence in their own self-worth, and how they think of their capabilities relative to others”. His point is that everyone has something to contribute, and he would like to help people worry less about what they don’t have — those gaps will be filled by the specific talents and expertise of others. The whole company organism can be much richer “if we recognize that we’re all different,” he says. By connecting to others with complementary skills, rather than shielding our true selves from criticism for our failings, “we can multiply our positive influence,” he explains.
If we recognize that we are all different, we can multiply our positive influence
Charles Lawrence, Global Quality Excellence Leader
The philosophy brings greater collective clout to all aspects of company capability, from problem solving to product design and quality improvement, and resonates with his own experience of living with the disability known as Asperger’s Syndrome.
Lawrence was relatively recently diagnosed with Asperger’s, which is now considered one of a variety of brain conditions on the autism spectrum. He had achieved outstanding career successes, but, as he wrote in a recent LinkedIn post, his difficulties in understanding other people’s emotional needs had led him to feel “defective”, and his sense of self-worth had hit rock bottom. He says he had always been driven to high performance by a fear of failure and being criticized and by what he perceived other people expected of him.
The diagnosis helped him understand that his brain is wired differently from the brains of most people (a 2020 study on autism in the US, for example, estimated that 2.2% of the population are on the autism spectrum), helped him reframe his challenges, and appreciate his own unique qualities.
He says that although he can’t compare his mental methodologies to those of others — “my only reference point is my own brain, I don’t know how other people think” — at work, he says, “I tend to focus on a really big picture and have huge aspirations as to where I want to get to.
“But I don’t mind which route I take. I’m very open to harnessing the power of diversity in people and engaging them to figure out how we’re going to get there.” He says he couldn’t care less about his own reputation but enjoys success through others — “and maybe that’s some of my different brain function”.
Lawrence believes an individual sense of self-worth can be fostered by greater honesty and openness about the challenges people face, how they experience life, and how they feel they can contribute. He says leadership is again key to creating an environment that values and welcomes diversity.
Perhaps similarly, the quality of organizational output relies on employees feeling comfortable — if not compelled by deep engagement — to identify opportunities for improving manufacturing systems, processes, and designs.
Product faults and failures don’t come cheap
One of W. Edwards Deming’s 14 points for total quality management, explained in his 1982 book Quality, Product and Competitive Position was to, “cease dependence on inspection to achieve quality.” It implies a system in which every employee takes responsibility for the products being produced, confident that they are working in an environment that backs them on striving for zero defects.
Lawrence chose this job for its “unique technology, diverse customer base, and most importantly for its great culture, and leadership that has a desire and courage to go on a significant quality-change journey”.
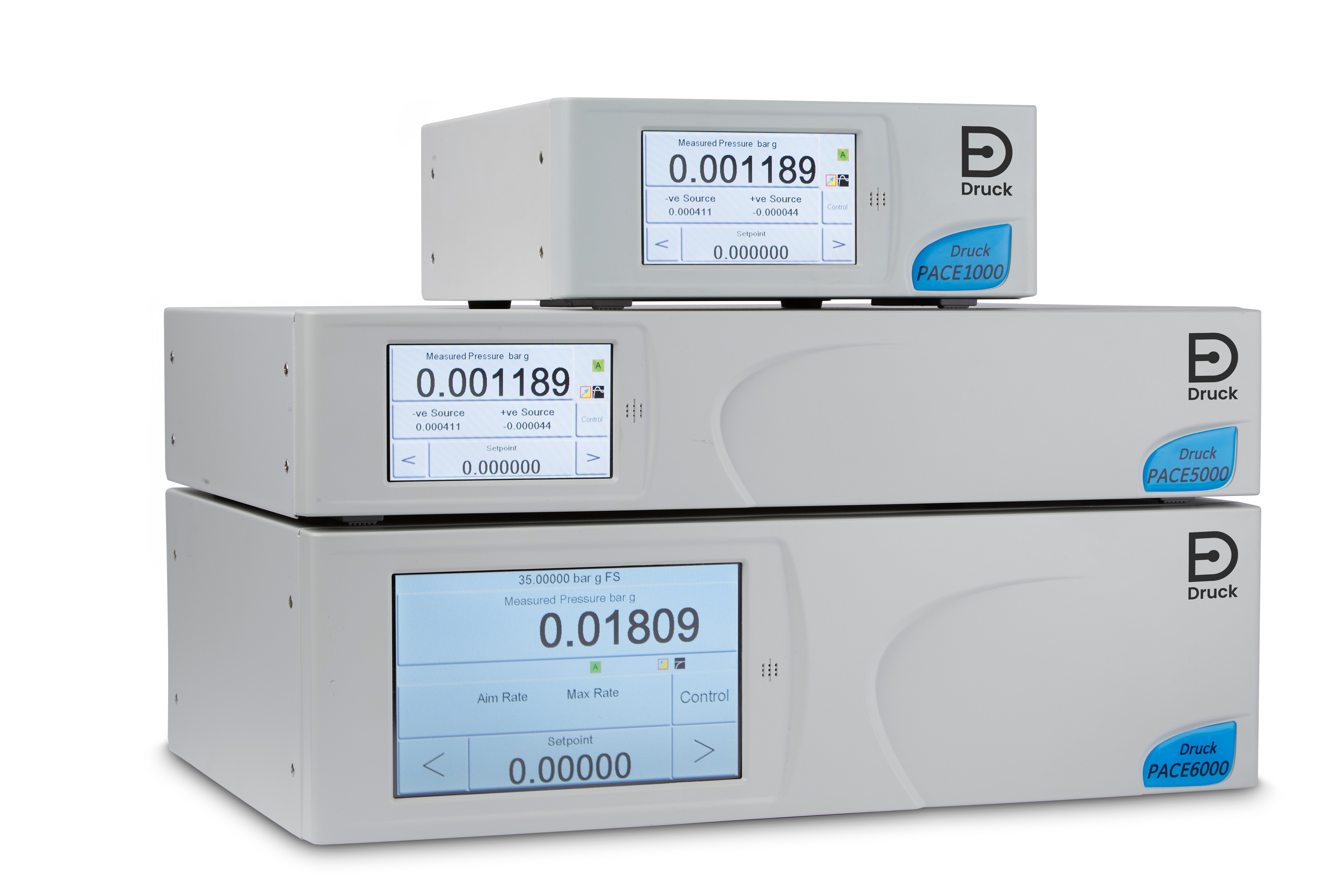
He intends to introduce coaching to grow employees’ capabilities to solve problems and improve output. Still, his underlying belief is that everyone has to be motivated to “go to the Gemba” — an anglicized version of the Japanese word “genba”, which means “the real place” or where the real action is happening.
That is, people focused on quality improvement get a truer perspective when they spend time on the manufacturing floor or sit in on a customer meeting. He says, “Then you can understand the difficulties, the problems, and opportunities — what the reality is. That’s when you tend to drive the right improvements, instead of decisions being based on someone else’s perception.”
Although leadership sets the scene for a zero-defect culture, Lawrence says lasting change occurs when every participant in product design, materials procurement, and manufacture “really wants to go on the journey, believing it’s possible to achieve zero defects and feeling more satisfied at the end of their working day because of how engaged they’ve been.”
Energy Forward Stories
Sign up to stay up to date on the latest innovations and people shaping the future of our industry.