Waygate Technologies’ ultrasonic thickness gauges are non-destructive testing (NDT) measurement tools used to inspect metal thickness and structural steel - which is essential across many industries, from Automotive and Aerospace to Oil & Gas and Manufacturing. Thickness testing is done in order to monitor for possible damage/defects during manufacture, as well as deterioration over time such as corrosion. Our ultrasonic thickness gauges are designed to provide accurate, reliable, and comprehensive thickness inspection data. We offer three industry-leading solutions for ultrasonic thickness measurement that are powerful, rugged, and easy to use.
The complex geometry of metal, steel, and plastic components often make it difficult to inspect with conventional gauges. Our market-leading ultrasonic testing solutions are engineered to help improve safety—ensuring the reliability of your equipment or material subject to corrosion or erosion.
Measure thickness with expert data analysis. Our devices are engineered to ensure the reliability of your equipment or material subject to corrosion or erosion.
Our Ultrasonic Thickness Gauge Solutions

DM5E Corrosion Thickness Gauges
Rugged, ergonomically designed, easy to use for measurements you can trust. Compatible with our best-in-the-industry probes, their ergonomic design and rugged housing are built to withstand even the harshest environments.
- Easy, intuitive operation takes thickness readings automatically, guiding you through every step
- Dedicated state-of-the-art probes allow for improved high-temperature performance
- DM5E and DM5E DL offer dual-multi measurement, allowing convenient measurement through protective coatings
- DM5E DL includes a built-in data logger supporting up to 50,000 readings

DMS Go+ Series A-Scan Thickness Gauges
Handheld instruments for thickness measurement, data recording, and data management for a wide range of applications and environments.
- Ergonomic design for easy operation
- High capacity data recorder and compatibility with powerful data management systems
- Intuitive arrow-keypad for positive digital control of parameters
- A “Flip” function allows use by both left-handed and right-handed operators
- Portrait or landscape views to match user preference
- A large 800x480 pixel display screen
- Small size, lightweight (870g, 1.9lb), robust construction to IP67 for operation in harsh environments
- Automatic gain control for excellent repeatability and corrosion monitoring
Find answers to the most often asked questions about UT thickness gauges:
An ultrasonic thickness gauge is a device used to accurately measure the thickness of a given material, typically steel, plastic, alloys, and the like.
UT thickness gauges are deployed in many industries but are most commonly used in Automotive, Aerospace, and Manufacturing to help ensure material thickness complies with production standards and their given industry's regulations.
UT thickness gauges can also be used as an additional quality assurance tool that helps to identify corrosion - particularly useful in the Oil & Gas industry where pipeline integrity is a concern.
Some models allow for the measurement of material through the exterior painted surface - thus removing the need for paint removal prior to measurement.
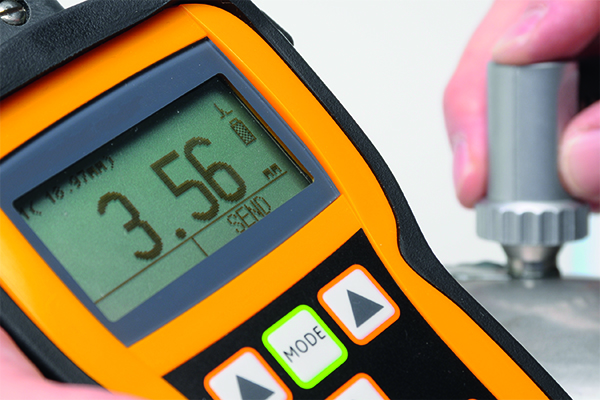
- Non-destructive testing (NDT) protocol means you don't have to sacrifice production samples
- Measurements can be taken without requiring access to both sides of the target material
- UT thickness gauges can measure through coatings
- A high degree of accuracy, typically around ~0.1 mm
- Perfectly suited to in-field testing, some models are rated for hazardous environments
- Relatively inexpensive to own and operate
- Some devices do not require the use of a couplant
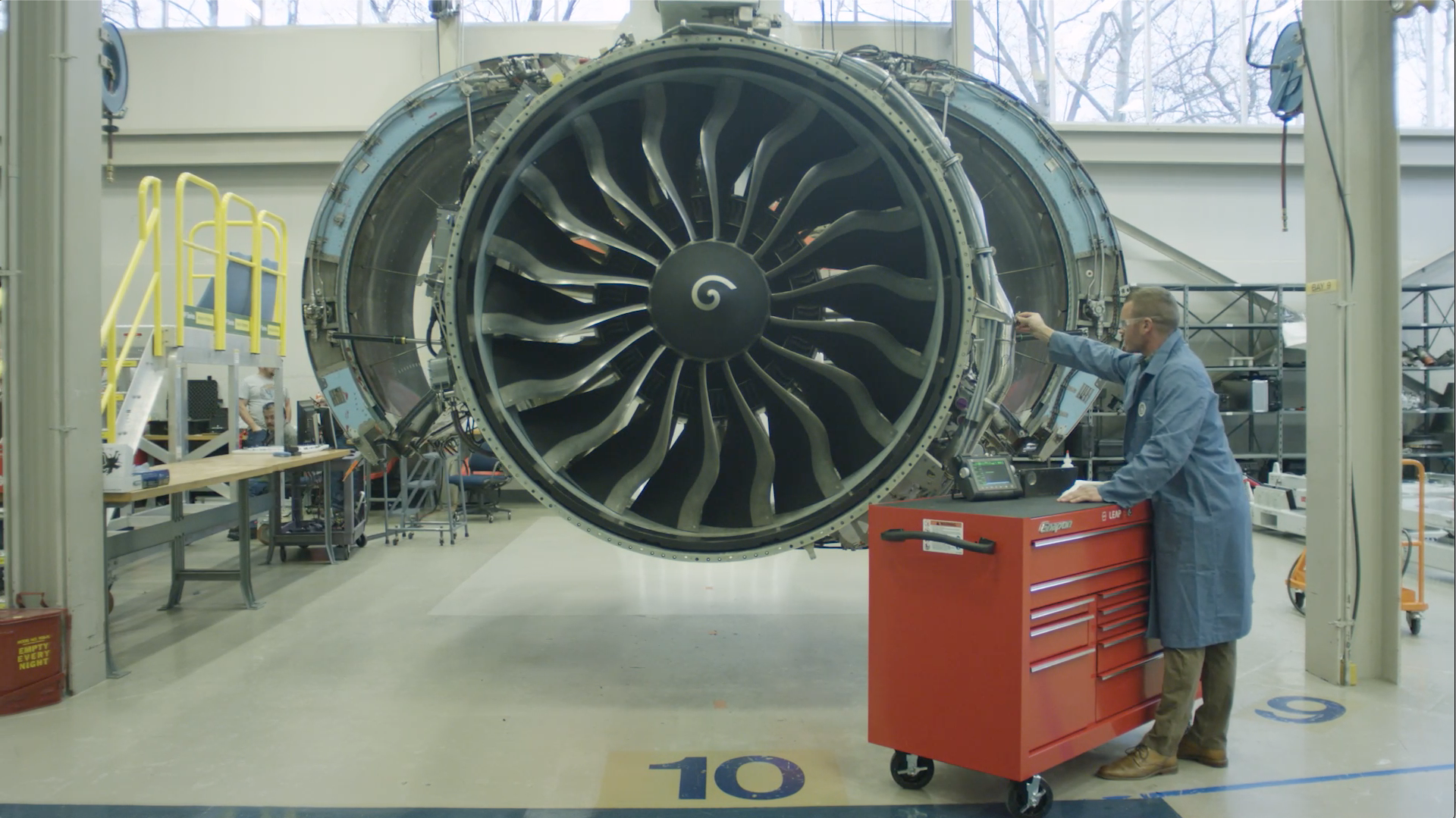
- Typically requires a separate calibration for each material being tested
- Accurate readings require good contact with the target material
- Some devices cannot take accurate measurements in the presence of surface rust
- Some devices require a coupling material between the target material and the probe
- Some level of technical expertise required to interpret results
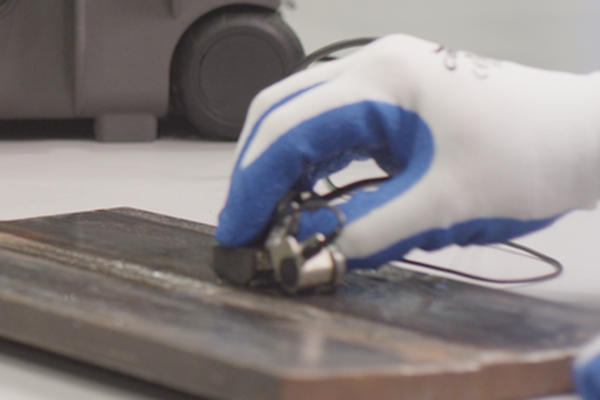
Ultrasonic thickness gauges are ideally suited for the inspection of material structures such as metals, ceramics, plastics, and composites. Industrial applications include:
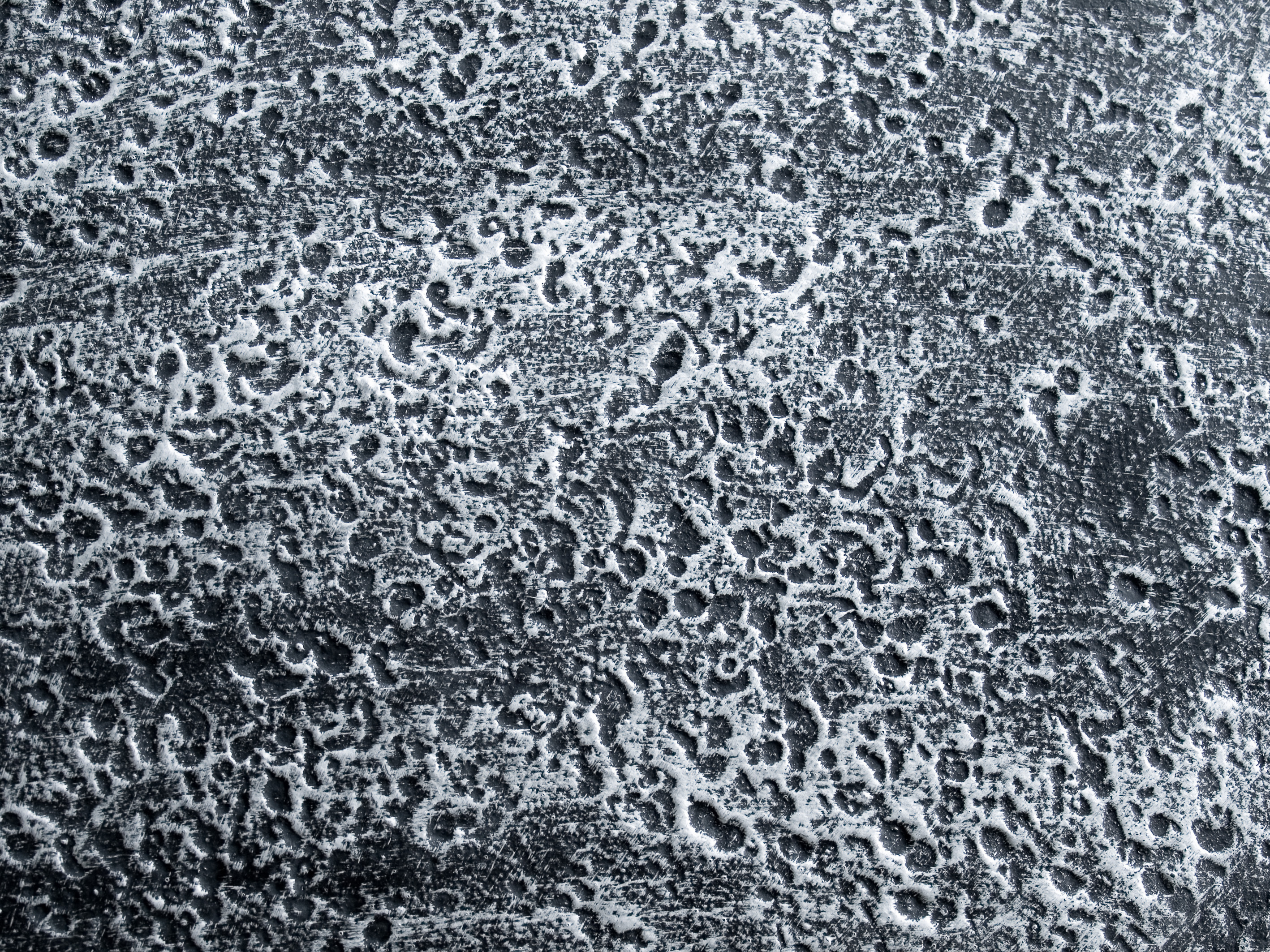
While there are several methods of calibration, such as One-point, Two-point, Auto or Manual On-block and Off-block Zero, Automatic V-Path correction, the underlying principle is that you will typically need to calibrate your device every time you switch your target material.
When using NDT equipment such as an ultrasonic thickness gauge, calibrations are performed via calibration blocks, also known as test blocks, that serve as a reference standard for a given target material.
Additionally, different calibration blocks can simulate different conditions, allowing the operator to calibrate for both the target material and conditional factors.
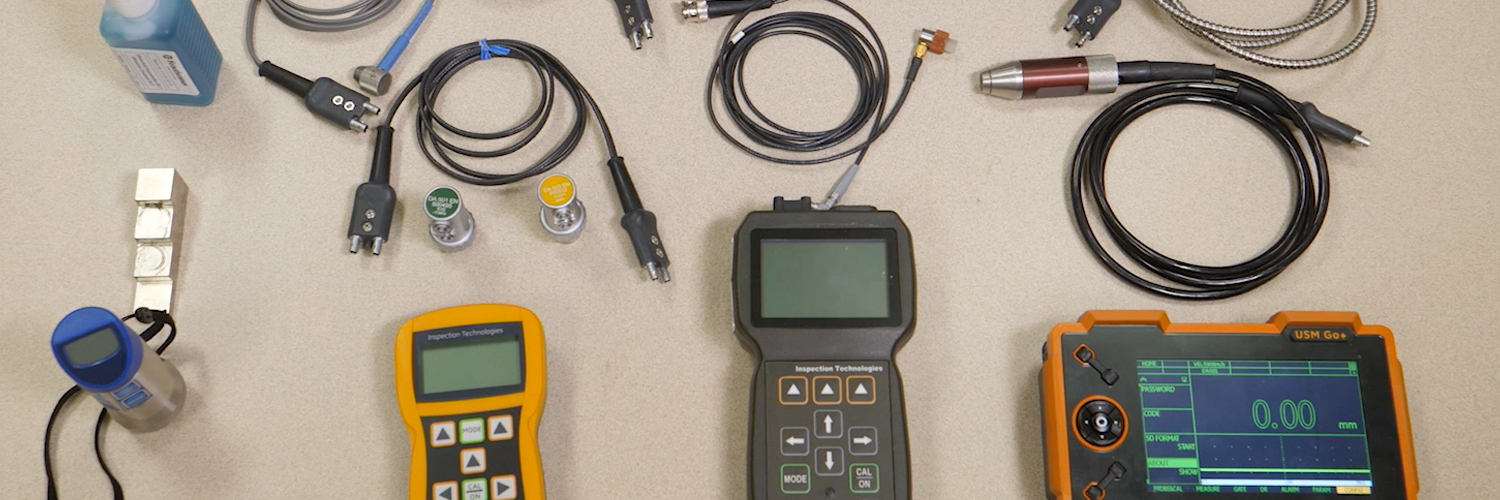
Some questions to consider when selecting the right ultrasonic thickness gauge for your application include:
- What factor (thickness, flaw detection, corrosion, erosion, etc.) am I testing for?
- What target materials do I need to be able to test for?
- Does my team require additional, specialized training to operate this equipment?
- What accessories (i.e. transducers, probes, couplant, calibration blocks, cases, etc.) are required? How much do they cost?
- What production and industrial standards am I testing to, and can the equipment test to those standards?
If you're unsure what device is best suited to your specific NDT needs, why not contact us and one of our UT experts will be happy to assist you.
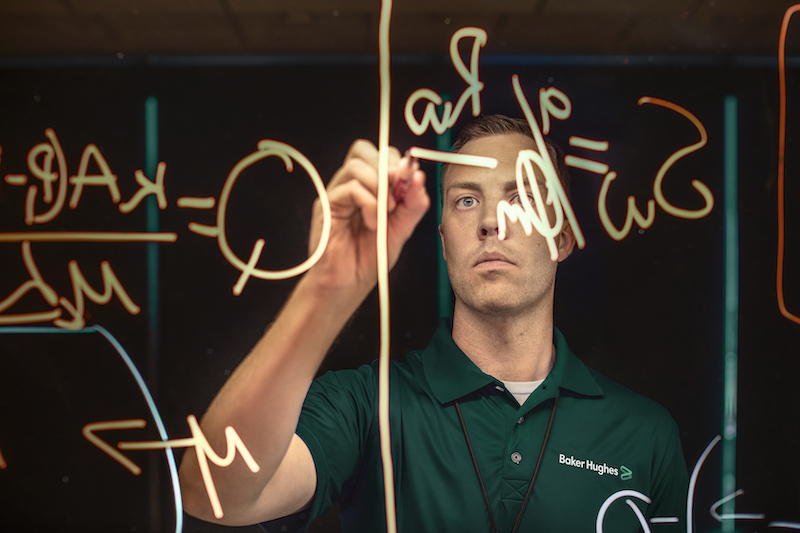
While there are several resources available for non-destructive testing (NDT) training, Waygate Technologies offers NDT training across the broadest range of inspection methods, which are offered around the globe, or at a location of your choice.
Get your team up to speed on how to most effectively use their ultrasonic thickness gauges today!
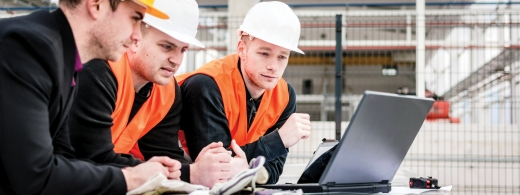